Cement Plants: Hg Monitoring for Peace of Mind
- libbyhancock7
- Sep 20, 2023
- 3 min read
The NESHAP rule for mercury emissions monitoring in cement plants, also known as the Cement MACT, has undergone more makeovers than a fashion model at a photo shoot. Since its introduction in 2010, the rule has been repeatedly revised and fine-tuned with amendments in 2013 and 2015, in response to industry feedback. These modifications have played a crucial role in clarifying and improving the rule but meeting the requirements outlined in the final version – which became effective in 2016 – can be quite a complex process. Now as EPA performs their Risk & Technology reviews, the MACT is being challenged again. However, one thing remains constant…the need to measure and report mercury.
In the cement industry, mercury concentration fluctuations can be extreme depending on raw materials and if the in-line raw mill is on or off. This is difficult for many real-time (PS 12A) mercury monitors to handle in terms of calibration and reliability. They require lots of highly skilled technician time for maintenance in order to pass the daily, weekly, and quarterly system integrity checks. Over the years, more and more cement plants have turned to mercury sorbent traps for compliance monitoring. For sorbent traps, concentration is no problem as traps simply capture the Hg over a period of time with no practical limit in their sorption capacity. Sorbent traps allow plants to report with average concentrations rather than divulge the peaks and valleys of plant emissions data which can be rather dramatic. Over and over, sorbent traps have proven themselves to be reliable, user friendly, and cost effective. But they still possess one major downside. They are not real-time and depending on the lab where they are analyzed, it can take days or even weeks to get results back. This certainly does not leave a plant operator with the warm and fuzzy feeling of knowing they are “in compliance.” For this reason, some cement plants have turned to sorbent trap change-outs two or three times per week. Though this is great for our business, it hurts our heart as we strive to make sorbent traps the optimal choice for the industries we serve.
But did you know there is another option?
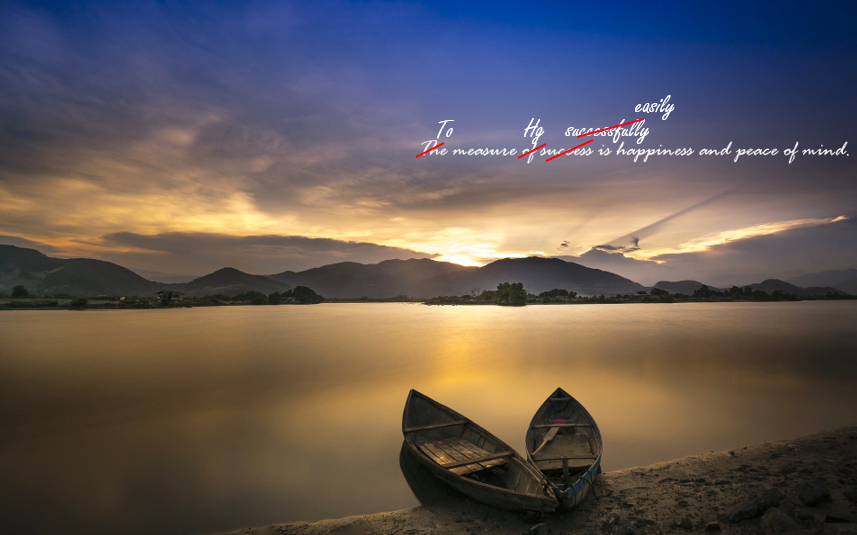
All the benefits of sorbent traps for compliance monitoring WITH mercury concentration data in real-time! The ability to change out your traps once a week without fear of being out of compliance!
Enter the 915J REAL-TIME Hg Process CEM!
A mercury process monitor paired with sorbent traps for compliance gives a plant the best opportunity at success from a mercury monitoring standpoint. A process monitor allows you to see in real-time what your sorbent traps see over the period of a week. This is beneficial because real-time feedback will allow you to notice any spikes in emission levels and allow you to fix the issues before it is too late. Moreover, if the plant utilizes any control technologies, the real time feedback from a process monitor will allow the operator to control the injection rate to ensure compliance while avoiding over-injection and thus realizing significant cost savings. The 915J has been specifically tailored to fit this function. It is extremely sensitive at low and high levels and measures mercury without any potential interference by utilizing Zeeman background correction technology. Alternative real-time compliance CEMs on the market are designed according to compliance method PS 12A and thus have certain limitations which lead to high maintenance and deficient sensitivity, among other issues. The simplicity and reliability of sorbent traps for compliance, paired with the sensitivity and low maintenance of the 915J Process Monitor offer the BEST chance for successful mercury monitoring.
I know…You must be saying it’s crazy to maintain 2 systems!
But, in reality, this dual approach is more reliable, more cost effective and less maintenance than using a PS 12A Mercury CEM.
Let us prove it to you! Please contact Alexandra for a presentation.
If you are not ready for a presentation yet, click here to read more on the 915J.